Last updated on October 13, 2023 by Morten Schiff
Article originally published in Fastener Technology International, February 2013
Testing underpins the fastener supply chain, from the fastener manufacturer’s basic fastener product performance and specification tests to the end-user Design Engineer’s bolted joint test rig and product testing. But testing in isolation has little value for fastener manufacturers, distributors and downstream original equipment manufacturers (OEMs). Design Engineers are increasingly integrating physical testing with software-based analysis to improve product safety and quality.
Vibrationmaster’s Morten Schiff and Bolt Science’s Bill Eccles explain the importance of integrating fastener and bolted joint testing with analysis during product design.
“When a Design Engineer specifies a particular fastener as part of a product design, there’s no question in his or her mind that the fastener will meet all the required standards for the specification. The expectation is that the fastener is correct,” explains Eccles, who regularly works with Design Engineers from leading OEMs across sectors such as automotive, aerospace, energy and construction, when delivering his training courses in the latest bolted joint testing methodologies.
Schiff agrees, adding, “Fastener manufacturers that can demonstrate an understanding of their end-user customer’s product design processes, and are able to create and implement their own testing strategies as a result, have the opportunity to create a source of competitive advantage. This can be a valuable strategy, particularly for fastener makers seeking to compete against low-cost fastener manufacturer entrants to their markets.”
Fastener Tests Using International Standards
The assumption by end-users that fasteners have been tested emphasizes the importance of testing samples during the fastener product development process. This ensures that each fastener’s physical properties meet the required specifications and expectations.
Basic testing of fastener properties by manufacturers is essential, because in Eccles’ experience OEMs rarely, if ever, test just the fasteners in isolation apart from for quality assurance reasons, whereas end-users focus testing resources on the performance of bolted joints.
The most common fastener standard for ISO-metric sizes, which incorporates testing methods for finished fasteners, is ISO 898-1: 2009 mechanical properties of fasteners made of carbon steel and alloy steel. The Industrial Fastener Institute (IFI) publishes similar fastener design and testing guidance for Unified threaded (UN) fasteners.
“ISO 898-1 describes nine tests (see below) for determining the properties of fasteners and includes detailed instructions on how to perform the tests, with what test equipment and which other standards apply,” says Schiff.
But as Eccles explains, it is not cost effective for a fastener manufacturer to test all its products to the full test regime for all fastener properties in every fastener size. In practice, manufacturers will provide test certification as required by their customer,” says Eccles. “Usually this is limited to proof load testing. Since it is their expectation that the fasteners will meet the relevant specification, most Design Engineers are unlikely to request test certificates for a manufacturer’s entire product range. In some high-performance applications, evidence of a rigorous testing regime can win a manufacturer a contract.”
Principal Tests for Fasteners (source: ISO 898-1:2009): |
Principal Tests for Bolted Joints (source: Bolt Science): |
• Tensile Test | • Friction Test |
• Proof Load Test | • Creep Test |
• Head Soundness Test | • Embedding Preload Loss Test |
• Hardness Tests | • Torque Tension Test |
• Decarburization Test | • Torque Angle & Torque-to-Yield Test |
• Carburization Test | • Vibration Test/Junker Test |
• Retempering Test | |
• Torsional Test | |
• Impact Test |
Testing Bolted Joints
While OEMs won’t test fastener products in isolation, generally assuming that the fasteners will meet the required specifications, they will test the performance of bolted joints.
“The level of testing performed by an OEM will depend on the product, its application and the production volume,” continues Eccles. “The end-user is seeking to design a bolted joint that will perform exactly according to specification and won’t fail. When bolted joints do fail, it is often the fastener that fails first. But further testing and investigation shows this is frequently not the case, and it is the installation process or the design of the joint itself, which is responsible for the failure.”
The result is a series of standard tests of bolted joints (see above for examples). These examine factors such as whether the joint is subjected to the correct torque, has undergone creep due to coated joint surfaces or self-loosened due to the effect of transverse vibration or embedding preload loss.
“These tests form an essential part of the product design process and are used to validate design decisions or to prompt redesigns,” highlights Schiff.
However, the complexity of many products prevents the physical testing of all bolted joints for practical reasons. Eccles explains, “If you consider a complex engineered product such as a car, each one includes hundreds of bolted joints with potentially hundreds of load cases, and it is not possible to test them all. At the design stage, each load case will be analyzed using analysis software that would be supported by tests that will be conducted to determine key parameters such as friction coefficient, creep or embedding preload.”
The parameters that have been determined by testing will be entered into the analysis software, which will further refine the specification of the fastener used for the bolted joint.
Integrating Design, Analysis & Testing During Product Development
“If you think of almost any engineered product, inevitably there will be a threaded fastener within the design, so the product will face failure issues that can arise as a result of using bolted joints,” says Eccles. “For example, a desktop computer contains screws that not only hold the device together, but some also provide the clamp force required to allow electricity to be conducted between two parts.
So loosening of these screws has obvious implications for the physical integrity of the product and can cause electrical problems with the device. Therefore, the Engineer designing the joints in a PC must design out self-loosening and other potential failure scenarios.”
It is also vital that Design Engineers identify any problems with product design early in the process. The closer to final production that problems are identified, which require design
changes, the greater the overall cost.
Weight, according to Eccles, is another key cost factor for product Design Engineers, and the test-analysis cycle is the tool typically used to optimize weight.
Over-engineering
“Over-engineering the design of a bolted joint by specifying a fastener that is larger, and therefore heavier, than required increases the weight and resulting production cost of
the product,” says Eccles. “The problem is made worse if a competing product incorporates leaner design, is lighter and therefore costs less as a result.”
The solution that product Design Engineers apply is an iterative and integrated product development process that incorporates both bolted joint testing and analysis. This approach enables Engineers to identify the optimal fastening solution at an early stage, which minimizes weight and cost, yet ensures product quality and safety.
Eccles, who has developed software that provides bolted joint analysis, explains how it works, “A Design Engineer will input the bolted joint parameters – which have been determined through initial testing and fastener product specifications – into the analysis software (see Figure 1a, 1b, 1c, and 1d).
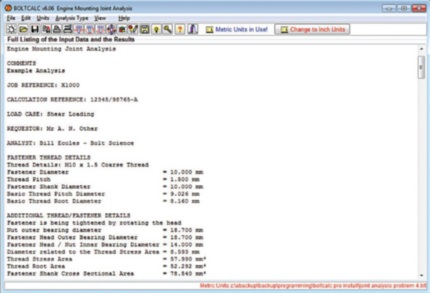
Figure 1a: Software screen from BOLTCALC from Bolt Science Ltd for an Engine Mounting Joint Analysis
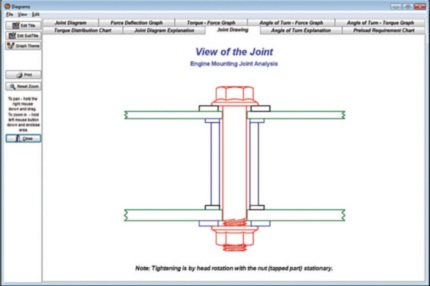
Figure 1b: View of the Joint from the BOLTCALC software
The output will be an assessment of the structural integrity of the joint. Essentially, the clamp force provided by the fastener should be such that, after allowing for preload scatter due to the tightening process and relaxation losses, the joint will not slip or separate under the applied forces.”
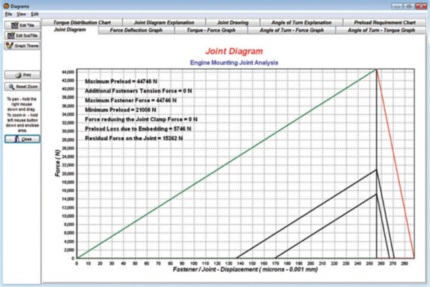
Figure 1c: BOLTCALC software screen of a Joint Diagram
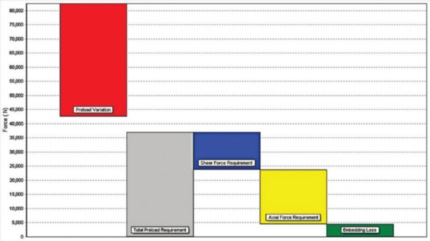
Figure 1d: Clamping force zones as calculated and presented by BOLTCALC by Bill Eccles
Testing Bolted Joints in Products & Test Rigs
Once the analysis has determined the type of fastener, torque and other features of the joint, the next stage is physical testing. Product development time pressures are such that testing is essentially proving the expectation that the product will meet all the performance requirements without any failures occurring. Failure on test is usually as a result of a failure of the analysis process.
The tests themselves can include rig testing of an individual joint under simulated loading or testing of the entire product using replicated service conditions. Key joints are often rig tested, as this allows Design Engineers the opportunity to test continuously, which is not normally feasible on a full product test. An advantage of rig testing is that the load signals applied to the joint can be edited and any quiet, low load periods can be removed. This way the joint can be subjected to an accelerated load regime 24/7. Some products lend themselves to this approach, but most don’t.
Eccles says, “For example, on low production volume products, it is not economically feasible to test the product under all possible load conditions. Even on high-volume products such as a car, testing the product under the hundreds of load cases is problematic and usually it is evaluated against a set of key loading conditions.”
Prototype building typically draws most experienced personnel
Another bolted joints testing issue is allowing for preload scatter. Prototypes are often built using an organization’s most experienced personnel. But it is desirable to test the product with the lowest anticipated joint preload. To achieve this, prototypes are often assembled using the lowest specified torque value. The bolted joint will be placed in a test rig, which will include the required sensors, load cells and load source required.
“The joint will then be subjected to the test, which could be any of the principal bolted joint tests such as vibration, creep or torque tension, depending on the Engineer’s requirements,” explains Schiff. “If the fastener and joint perform according to specifications, then it can be adopted into the overall product design.”
However, if the joint fails during testing, additional testing and analysis will be conducted to find the cause. A new bolted joint design will be developed, which may incorporate an alternative fastener and changed parameters such as increased torque or locking element.
Fastener manufacturers and distributors have a vital role to play in the product design, testing and analysis process. Design Engineers require access to a huge range of fasteners with the right characteristics to meet design specifications.
By designing, testing and producing a broad range of high quality fasteners with wide variations in specifications and performance, fastener manufacturers can meet this need.
About the contributors…
Bolt Science provides independent technical expertise in bolted joint technology. Software products include bolted joint analysis, torque tightening and fastener failure programs. Bolt Science delivers a range of training courses to fastener manufacturers and downstream OEMs on bolting technology and analysis. Consultancy services include creating analytical solutions to bolting problems, joint and fastener testing and expert witness services. Based in the UK, the firm operates globally, with clients from the fastener sector and across all major industrial and engineering areas. www.boltscience.com
Vibrationmaster designs/manufactures advanced testing technology and delivers specialized test services. Products include Junker Test machines to analyze/demonstrate self-loosening behavior of fasteners and bolted joints to DIN 65151, DIN 25201, and ISO 16130. With a head office and R&D function in Luxembourg and advanced manufacturing facilities in Germany, the firm operates globally. Customers span the commercial, academic, research, public, government and not-for-profit sectors. We offer highly reliable test solutions to organizations seeking market-proven and cost-effective technology to test and prove reliability, consistency and safety of their products. www.vibrationmaster.com